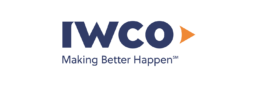
Business Profile
IWCO is a leading provider of data-driven direct marketing solutions. The company’s full range of services includes strategy, creative, and execution for omni-channel marketing campaigns, along with one of the industry’s most sophisticated postal logistics strategies for direct mail.
Industry
Print Service Bureau
Solving Challenges in a Mixed Vendor Shop with Solimar Systems
Watch the Case StudyOverview Video
SOLitrack Unlocks Speed, Visibility for IWCO’s Workflow
Introduction
Staying at the cutting edge of technology to delight customers is the hallmark of IWCO. For more than 50 years, they have been at the forefront of helping clients create winning marketing strategies by finding their audiences, developing creative content in physical and digital formats, and delivering it through effective campaigns. Solimar Systems’ Chemistry™ platform is helping them stay in the lead.
That staying power requires IWCO’s print operations to stay current with best-in-class printing equipment from a variety of vendors to meet the diverse needs of their client base. IWCO takes a multi-vendor approach to source the best technology for their range of print applications, including a recent $50 million investment intended to grow their performance marketing solutions. As part of that investment, IWCO is adding multiple HP PageWide Web Presses to its existing fleet of Canon and SCREEN high-speed inkjet printing solutions, which requires a flexible, extensible set of workflow tools.
IWCO Case Study: Solving Challenges in a Mixed Vendor Shop with Solimar Systems
SOLitrack Unlocks Speed, Visibility for IWCO’s Workflow
Annette Friskopp, Vice President and General Manager, HP PageWide Industrial Printing shares: “IWCO has made amazing progress since installing their first HP PageWide Web Press in September 2021. They have rapidly ramped up to five presses and are one of the largest producers of delivered marketing materials.” Friskopp continues, “HP and Solimar have partnered together to provide a path to continuous improvement for our mutual customers, including some of the largest print service providers.”
At-A-Glance
Locations (USA)
- Chanhassen, MN, USA
- Hamburg, PA, USA
Business Solution
Solimar Products
Benefits
-
- Eliminated the need for machine-specific workflow solutions to feed digital front ends (DFEs)
- Saved 7.5 hours per day using a new quality control job batching process
- Avoided nearly $110,000 in equipment replacement costs using a digital re-engineering solution
- Post-composition scale and shift process dynamically handles chipout requirements for various output devices
- Automated positioning of chipout areas saved $85,716
“We were able to quickly make these adjustments to our workflow, saving $85,716 taking the digital approach.”
Tony Picciano
Applications Engineer, IWCO
From Many Workflows to One with Solimar
Such a diverse set of printing equipment allows IWCO operational flexibility, but it traditionally meant machine-specific workflow solutions feeding dedicated digital front ends (DFEs) to manage. IWCO found a better way to manage its complex workflows regardless of the equipment using solutions from Solimar Systems. Solimar’s SOLfusion™ receives input primarily from IWCO’s long-standing composition tool Quadient Inspire, then powers the workflow tasks, including file conversions (AFP, PostScript, PDF). When needed, SOLfusion seamlessly passes files to Solimar’s Rubika® document re-engineering tool for page and layout level adjustments before sending the files to Solimar® Print Director™ Enterprise (SPDE) for management and output to the printers. “Having a unified and centralized solution to manage and output files for our diverse set of printing equipment has been tremendous in our ability to meet our SLAs,” says Carroll Schiley, Director of Production Technology Applications at IWCO.
The Ultimate Quality Control Upgrade
When it comes to the integrity and accuracy of data, IWCO has relied on continuous improvement to its quality control (QC) programs. QC programs ensure customers get their intended direct mail without inserting duplicates into the postal system, risking fines and unhappy clients. Before Solimar, IWCO relied heavily on the equipment operators to print a predefined number of records from the loaded job, review for quality, discard those prints, and restart the job for printing for every single print run.
Using Rubika, IWCO can batch records from multiple jobs using the same paper, apply a watermark, print the samples for QC, and then start the production run for all the batched jobs. The total number of processing steps was reduced along with the amount of QC time needed for each print job. Printer idle time is less, which increases the print capacity per shift. According to Tony Picciano, Applications Engineer at IWCO, “The new QC process using Solimar tools saved us 7.5 hours per day.”
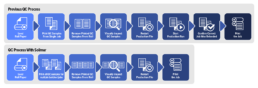
The Chemistry Solution
The Digital Solution to a Physical Equipment Challenge
When IWCO installed the new HP PageWide Inkjet Web Presses, the margins needed for barcodes and other marks for the press were a half-inch different than the existing equipment. This chipout area is printed but then removed with in-line cutters. While a half inch may not seem significant, the difference would force upgrades to many of the cutters that relied on fixed blades to variable blades at the cost of approximately $110,000. The first attempt at a digital solution was to change the templates in the composition tool. This approach was quickly abandoned due to the time and complexity of updating thousands of customer files.
The more efficient solution was to adjust the file post-composition using Rubika. With the assistance of the Solimar support team and further testing, IWCO was able to combine several functions like scale and shift to automate the adjustments needed to have the correct positioning for the chipout areas. They also handle the different chipout areas for the front versus the back printed sides when MICR is used. Picciano notes, “We were able to quickly make these adjustments to our workflow, saving $85,716 taking the digital approach.”
"Having a unified and centralized solution to manage and output files for our diverse set of printing equipment has been tremendous in our ability to meet our SLAs."
Carroll Schiley
Director of Production Technology Applications, IWCO
A Partnership, Not a Vendor
Both Schiley and Picciano attribute the success of the new QC program and solution to the chipout issue to Solimar’s dynamic support team. Unlike other vendors where a ticket gets submitted to a queue and hours or days pass before getting a response, Solimar’s support staff is responsive and proactive in finding solutions to business challenges, not just issues related to their software. Schiley went on to say, “With Solimar, it feels more like a partnership than the typical vendor relationship.” IWCO is looking forward to leveraging the partnership and leveraging more of Solimar’s Chemistry platform to support and grow their business.