Business Profile
Lasertec supports its clients with statement printing, electronic document delivery, notices, tax forms, target marketing, selective inserting, graphic design, and other document related services.
Industry
Print Service Provider
Location
Sterling Heights, MI
Business Solution
- Job scheduling management to satisfy Service Level Agreement criteria
- Operational control and standardization
- Maximize use of printing equipment and resources
- Ability to accept and process all required incoming file formats
Solimar Products
- Solimar® Print Director™ Enterprise
- Queue Manager
- Rubika®
- SOLindexer™
- SOLfusion™
Benefits
- Reduced development costs by $100,000 per year
- Reduced labor expenses by $50,000 per year
- Increased output productivity
- Ability to dynamically add barcodes and underlays
- Increased workflow automation and efficiencies
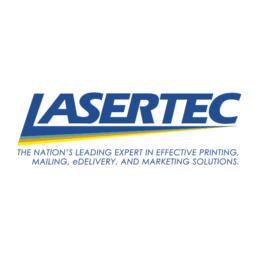
Solimar Helps Lasertec Reduce Manual Operations and Costs
Lasertec, Inc. was founded in 1986 to provide affordable high-speed laser printing and mailing to financial services organizations, primarily credit unions. As Lasertec grew in size and assets, their services were offered to many other industry types, including: healthcare, insurance, automotive, government, industrial, and advertising agencies. Today Lasertec supports its clients with statement printing, electronic document delivery, notices, tax forms, target marketing, selective inserting, graphic design, and other document related services.
Lasertec’s main production facility in Sterling Heights, Michigan opened in 1998. With nearly 40,000 square feet of space, this facility operates 24 hours a day, 7 days a week during peak production times. In July 2009, Lasertec opened a second facility in Auburn Hills, Michigan. This second facility serves a dual role that provides incremental capacity production in addition to being a valuable disaster recovery backup site.
Lasertec has had over 25 years of successful client partnerships with hundreds of businesses nationwide offering a full array of high-quality printing, mailing, electronic document delivery, and marketing services. Lasertec continues to expand its capabilities, increase efficiencies, and remain a leader in the printing and mailing industry. For two consecutive years, Inc. Magazine has selected Lasertec as one of America’s Fastest Growing Companies.
Solimar Systems interviewed Jim Jones, Executive Vice President of Production at Lasertec to discuss how implementing Solimar technology has expanded capabilities, increased output productivity and reduced development and labor costs.
“Our Solimar solution saves us $150,000 per year in development and labor costs.”
Jim Jones
Lasertec, Inc.
The Challenge
Lasertec continually monitors its internal business process looking for opportunities to improve its operations. Lasertec performs regular self-assessments of their production workflows to evaluate and explore various ways to improve their overall efficiency and productivity. After a thorough examination of their document related business operations, they uncovered workflow areas that they felt could be streamlined. The specific production challenges Lasertec discovered for improvement were:
- Inefficient methods to add color document underlays
- Limitations to accept, process, print and archive certain data stream types
- Lack of uniform standardized processes
- Slower than desired client project turnaround time
Once the challenge areas were identified, Lasertec began the process to address them by researching technology solutions. “We wanted to implement software automation in areas where we felt it made the most sense,” said Jones. “Our focus was on improving areas where we could replace recurring manual operations with automation to achieve greater production efficiencies with sustained economic ROI benefits.”
The Solution
Lasertec was aware of Solimar’s strong reputation and expertise as an output management software solution provider. As an existing Solimar® Print Director™ Enterprise (SPDE) user, Lasertec was also familiar with Solimar’s other complementary products that could address the production areas requiring improvements. “Because we had an existing client-vendor relationship with Solimar, we felt very comfortable having them help us with our needs,” said Jones.
SPDE provides a streamlined user interface for Lasertec with a consolidated view that allows their print operators to monitor and control print queues and jobs. This allows them to initiate and halt job processing, reorder and move jobs between queues, handle reprints, and interventions based on the security rights assigned to them.
“With our Solimar solution in place we can now print our legacy LCDS jobs on virtually any printer,” stated Jones. “This gives us a lot of flexibility with job scheduling and helping us meet critical SLAs.” The SPDE Queue Manager’s highly customizable user interface allows Lasertec operators to create individual “views” that organize the queues and jobs according to their preferences, and filter messages based on user-defined rules.
Lasertec decided that Solimar’s Rubika® solution along with SOLfusion™ would provide the desired workflow automation capabilities that they needed for document re-engineering and optimization. Using Rubika’s various document re-engineering modules, Lasertec was able to significantly decrease the application set up and development time required for client projects.
Rubika’s graphical user interface allowed Lasertec’s production team to rapidly prepare client projects prior to printing. “Rubika has reduced the need for our development staff to create custom code,” said Jones. “Rubika has reduced the complexities of making data stream modifications by simplifying it with an intuitive interface. Rubika allows us to develop applications more rapidly and at a lower cost. Our document re-engineering workflows are much more efficient as a result of Rubika.”
“Rubika allows us to produce full color transactional documents without the need for preprinted stock.”
Jim Jones
Lasertec, Inc.
The Results
Lasertec has leveraged their Solimar solution to automate costly manual processes. “Our Solimar solution saves us $150,000 per year in development and labor costs,” said Jones. “We also believe there are still untapped solution capabilities that will give us additional future value and provide us with even more workflow efficiencies. In addition to reducing our costs, we have been able into increase our output production by 15% by load balancing our infrastructure. Solimar’s data stream transforms have allowed us to better utilize our printers. We can now send our print jobs to virtually any printer.”
The Rubika solution provides Lasertec the ability to easily add full color image underlays to documents that previously required preprinted stock. “Rubika allows us to produce full color transactional documents without the need for preprinted stock,” said Jones. “This has saved us warehouse space and obsolescence costs. From an operational perspective, it allows us to make changes much more quickly and easily, and the print operators are now more efficient since they no longer have to track down the required preprinted stock for the job. This also reduces the chance of the operators using incorrect stock, which delays projects and increases costs.”
Rubika’s document re-engineering capabilities have also provided Lasertec efficient methods to easily add Intelligent Mail Barcodes (IMB) and 2D barcodes to documents. “We are now able to update our legacy jobs to match our new document applications much quicker,” stated Jones. “This significantly reduces the potential for human error and helps us standardize our production workflow processes.”
Lasertec has also been very happy with the post-sale technical support they have received from the experienced Solimar staff. “The technical support staff is very knowledgeable and helpful concerning all our Solimar products,” said Jones. “When we need help, they always have a fast, accurate and courteous response.”