Business Profile
Long established service bureau implements Solimar solutions to reduce costs, gain new production functionality and increase automation.
Industry
Service bureau
Locations
Niles, IL
Business Solution
- Implement greater production print control
- Post-composition document enhancement
Solimar Products
- Rubika®
- Solimar® Print Director™ Enterprise (SPDE)
- SPDE Queue Manager
- SOLfusion™
- Solimar Indexing Tools
Benefits
- Faster turnaround for damaged re-print workflows
- Reduced IT labor costs by 15% for spoilage workflows
- Increased automation reduces processing time by 90%
- Fewer departments and fewer personnel hours are needed to produce reprints
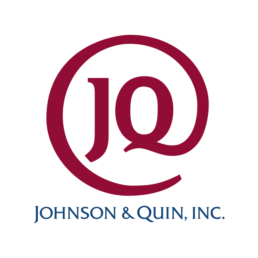
Johnson & Quin Adds Rubika® to Existing Solimar Solution Suite
The original company roots began in 1876 in the Chicago metro area and have since prospered by deploying the latest customer communication technologies while adapting to the changing marketplace. As an industry pioneer, Johnson & Quin led the introduction of laser printing to the Midwest region of the United States, which soon transformed them into a full-service direct mail production company.
Using a broad range of capabilities, Johnson & Quin is an excellent resource for projects ranging from on-going direct mail programs and customer communication programs to large projects involving several million mailpieces. They particularly excel at complex projects with personalized and variable data printing.
Johnson & Quin offers the latest in integrated marketing solutions, as well as data services, personalization technologies, quality processes and certified data security practices. The innovation, flexibility, and solid financial credentials that propelled Johnson & Quin throughout their history remain at the core of the way they work and operate today.
During recent years, Johnson & Quin has leveraged the benefits and value of the Solimar® Print Director™ Enterprise (SPDE) system for their operations. The SPDE system has served Johnson & Quin well by utilizing advanced technology enabling customer communications workflow automation. The SPDE system combines multi-level security, remote administrator and operator access, event logging, notifications, direct device connectivity capabilities, powerful job routing and tracking with industry-leading data stream transformations.
Solimar Systems interviewed Manish Haria, CIO & CISO at Johnson & Quin to discuss their decision to add the Rubika® product to their existing Solimar Systems solution suite.
“The automation resulting from Rubika reduced our reprint workflow costs by 90%.”
Manish Haria, CIO & CISO
Johnson & Quin
The Challenge
Johnson & Quin had been primarily using the AFP output file format for the better part of the last two decades. However, with their recent switch to high speed color inkjet printing, they made the migration to the more modern PDF-based data stream as well. As they became more familiar with the PDF format and associated workflows, they began to realize how post-composition functionality could be leveraged to benefit them.
A significant objective Johnson & Quin wished to achieve was modernizing the damaged pieces reproduction workflow in addition to improving data integrity. There was a portion of their work that required spoilage reproduction on a sizeable scale and for that work, the existing workflow was somewhat inefficient and error-prone requiring multiple departments to be involved.
Spoilage needed to be captured to a file on the production floor via handheld scanners. That file was interrogated to select affected records from the data file so they could be processed through the document composition software a second time. There was extra effort, time and expense required to make sure that the reproduced pieces matched the original composed pieces sent to production. This was especially onerous and disruptive for the current campaigns that were still in manufacturing while IT was working on the next upcoming campaign. “This process was error-prone and required multiple departments with checks and balances to ensure accuracy,” said Haria. “We felt there was room for workflow improvement and began looking for ways to implement improved efficiencies.”
The Solution
For several years, the existing SPDE system has given Johnson & Quin the ability to print from multiple host computers to multiple printing devices simultaneously. SPDE also performs multiple conversion routines on each print file when needed. By supporting various combinations of inputs, outputs, and conversions, SPDE gives users a powerful print manager that transparently connects host systems with the production printers. As requirements grow, SPDE users can easily add software modules, install additional inputs and outputs, or upgrade to take advantage of new features and capabilities.
But what about document enhancement? “Rubika was the natural choice for us to evaluate for post-composition workflow,” said Haria. “Once we trialed Rubika – we used it and saw what it could do for us – we liked the features it offered us and proceeded to acquire it.”
Rubika is a modular solution with robust capabilities to automate manual processes, enable postal savings, add value to documents, and modify print data on-the-fly. Using Rubika, transactional content can be applied to add significant value to customer facing documents without complex programming.
Rubika requires no coding at the application level and provides an intuitive user interface to rapidly implement document enhancement production changes. Rubika is used to solve a variety of workflow challenges and can be configured in many different ways to increase efficiencies and profitability.
Johnson & Quin uses Rubika to select the PDF ranges for spoiled pages thereby providing ultimate piece-level integrity. This eliminated potential errors due to campaign overlap in IT and manufacturing. The data processing department involvement was eliminated from the workflow and the need to keep large datasets on primary expensive IT infrastructure was greatly reduced.
“Rubika helped us realize close to 15% savings in IT labor.”
Manish Haria, CIO & CISO
Johnson & Quin
The Results
Using Rubika, fewer departments and fewer personnel hours are needed now to reproduce spoilage. Additionally, it helped cut down on labor hours needed on processes to ensure spoilage reproduction accurately matched production. Rubika has helped Johnson & Quin realize about 15% savings in IT labor for the work involving print spoilage.
Once all the automation is completely realized, the time savings from initiation to completion of spoilage workflows will be reduced by 90%. “The intangible savings have been the peace-of-mind in knowing that reproduced spoiled pieces are truly just being reprinted and aren’t being recomposed,” said Haria.
With Rubika, we have been able to achieve greater efficiencies and eliminate data integrity errors for spoilage. The involvement of more expensive departments like IT has been reduced by 50% with a near-term goal of removing 80% of manual touches.
Haria explains that Solimar’s documentation and help manuals are very useful in understanding the individual products and clarifying where each product fits in the common workflows along with detailed technical features.
Haria said, “Solimar’s technical support staff has been excellent at servicing us, very prompt and knowledgeable. Solimar is a team of professionals that keep on top of issues, keep us abreast of the progress and follow up afterwards to ensure the issues stayed resolved.”
“Solimar’s management and support teams have stepped in to help even when we have called upon them for help with issues outside of the scope of their expected services and they have always been willing to help with their technical expertise,” Haria added. “This is the way technical support should be, but sadly it is rarely encountered these days.”