Maximizing Printer Placement: Six Workflow Considerations
Welcome to our session on “Six Workflow Considerations When Placing a New Printer.” With over three decades of experience collaborating closely with printer vendors, Solimar understands that integrating a new printer offers a gateway to business expansion, heightened efficiency, and amplified profits. Yet, it also presents challenges. Today, we’ll navigate through these challenges and unveil how Solimar can provide effective solutions.
Evaluating the Printer Transition
As you embark on the journey with your new printer, it’s pivotal to ask essential questions that guide your progression. Introducing new equipment prompts a reevaluation of current operational methods and identifies areas for potential improvements.
Print Streams and Formats
While many operations need the luxury of choosing their received print streams, introducing a new printer signifies an opportunity for transformation. Recognizing that most printer and workflow vendors prefer PDF as the go-to print stream, Solimar emphasizes the significance of PDF in facilitating color and graphic rendering, subsequently enhancing user experience and versatility.
Transformation Location
The decision on where to execute transformations is a critical choice. Centralizing transformations in distributed print operations grants superior consistency, control, and flexibility. The Solimar Print Director Enterprise (SPDE) system seamlessly transforms various formats, ensuring comprehensive coverage and efficiency.
Onboarding and Work Transformation
Onboarding new or existing work to a new printer can vary in complexity. Solimar’s Rubika software streamlines and adapts jobs for optimal performance and compatibility, ensuring a seamless transition to the new printing environment.
Content Enhancement and Batch Processing
Need post-clean-up of input files? Solimar’s solutions offer many options to enhance content, such as color tuning, optimizing resources, and batch processing for higher production print efficiency. This facilitates streamlined management of diversified workloads and optimizes postal processing software for automated sortation and mail optimization.
Job Release and Production
Upon content optimization, jobs are released into production, binding specific production processes to jobs with accuracy and efficiency. Rubika is a versatile tool for job engineering and customization, whether through fully automated lights-out processes or manual intervention.
Cut Sheet Printing Advantages
Solimar understands the complexities of tray pulls and inline finishing in cut-sheet printing. Rubika simplifies transferring work across different devices while maintaining finishing consistency and compatibility by ingesting and modifying finishing information.
Transition to Full-Color Inkjet
Moving to full-color inkjet printers opens a realm of possibilities. Solimar emphasizes shifting towards the white paper factory workflow, offering streamlined and cost-efficient processes without relying on preprinted stocks.
File Size and Workflow Efficiency
With increased print volumes and larger file sizes in mind, optimizing PDFs within the workflow becomes essential. Solimar’s PDF optimization tools, like ReadyPDF, ensure file efficiency and quicker RIP times, boosting overall workflow performance.
Output Management and Job Tracking
Solimar’s SOLitrack software provides comprehensive output management capabilities, effectively tracking jobs, pieces, and processes within operations. It offers an integrated dashboard for job tracking, automation, and data analysis, empowering organizations to make informed decisions for process improvements.
To summarize, navigating the transition to a new printer involves addressing multifaceted workflow considerations. Solimar Systems’ suite of software solutions in the Chemistry platform, including Rubika, SPDE, and SOLitrack, offers a comprehensive toolkit to streamline operations, optimize print workflows, and enhance overall efficiency.
Hello, welcome to this session, Six Workflow Considerations When Placing a New Printer. Solimar has worked closely with printer vendors for over 30 years. Placing a new printer opens up new opportunities to grow your business, improve efficiency and profits. It can also present challenges. Today, we’re going to talk about some of the challenges you may face and how Solimar can help.
Congratulations on your new printer. Here are a few questions you should be asking yourself as you move forward. Any time you introduce new equipment into your environment, it gives you the opportunity to consider why you do things the way you do.
One of those things should be which print streams you use in your operation. Many operations don’t get to choose which print streams they receive. They get what they get. You just need to deal with that.
This diagram shows a pretty standard production workflow. Inputs are received in a variety of formats and are optimized for production. They are then transformed into formats specific for printing, epresentment and archive. While you may not have a lot of control over what you get, you do have control over the outputs, especially when placing a new printer. Right now, most printer and workflow vendors have settled on PDF as the best go forward print stream. PDF also drags JDF along with it as the preferred protocol for submitting jobs to PDF printers. IPDS is a capable and a traditional leader in transactional work. But PDF is generally considered better for color and graphic rendering. Other formats like PostScript and VIPP are still viable but are not quite as strong as PDF as a standard format. PDF is the one format you can easily view can be used for proofing and is ubiquitous in the market. This makes it an easy choice.
Another decision point is around where to do transformations. The options here are to use a centralized server or to use transforms available at your printers or DFE. For shops with one or two printers, doing transforms at the printer or DFE may make sense. However, there are challenges. Monetary challenges. You need to buy the transform for each DFE. Consistency issues. If you use a different DFE, even from the same vendor, you may get different results across printers. And, from a workflow standpoint, centralized transforms allow you to distribute output wherever you want without regard to whether there’s a transform available there. Most large operations choose to centralize transformation in distributed print. This provides better consistency, control and workflow flexibility. One way to do that is with SPDE. SPDE can transform from, and then to, just about any format. This table shows the transforms available within SPDE. As you can see, we’ve got you covered.
Onboarding new or existing work to a new printer can be very simple or it can be very complex. It really depends upon what you get and the complexity for each workflow. We saw in the last section how jobs are ingested into the system, typically with a transform into a standard format. For Solimar, this is PDF. Most organizations strive to have a single uber workflow for all work. This workflow is tracked, monitored and has controls built right in. Making all work look the same has huge benefits for operations. There will always be unicorns out there, but you don’t want to have to deal with a whole herd of them.
It is very likely that your new printer is significantly different from what it is replacing. This means that files will need to be reworked. Many times, existing jobs are built for existing print, finish, and distribution processes. These are commonly known as print ready files. The file may include things like barcodes, finishing marks, and it may be imposed. These things tie the job to specific print production process and may need to be removed. If the file is already process neutral, you’re good to go. If it is not, you may have your work cut out for you. Fortunately, Rubika is very good at this.
Once you have clean, uniform input files, there are a lot of things you can do with them. You can enhance the content by adding color, replacing logos, adding transpromotional material, deleting or adding blank pages, and more. For jobs that were previously cut sheet using preprinted shells, underlays can be added to replace them, if you plan on printing them in color. More on that later. Process neutral jobs can be batched with like work for further production efficiency. Making a lot of small jobs into one big job makes managing work much easier. Jobs can use postal processing software to perform sortation, National Change of Address, and other postal optimizations. This is especially effective with jobs that are batched together.
Once output is optimized, it can now be released into production. When a print, finishing and distribution plan is selected by the operator, the job is released and the job can be re-engineered for that specific process. This binds the production process to the job, so the job ends up much like the process specific jobs we started out with, except this time, it’s your process. This is usually done as part of a fully-automated lights out process, but you can always choose to put the job into a queue and let operations make the call on how to process the job based on the current availability of equipment, staffing and schedules. In that scenario, operations is empowered to decide when and how to run a job in their plant based on the conditions on the ground. Rubika does all of that. Rubika is a Swiss army knife for job engineering. There’s something you need to do, chances are pretty good Rubika has a number of different ways to get it done.
One of the superpowers of cut sheet printing is the ability to handle tray pulls and inline finishing, producing finished work off the end of the machine. Moving work to different machines while maintaining tray pulls and finishing can be a tricky business. Why is that? It’s because methods for handling finishing are really important capability are a mess. There’s no real dominant method for managing this across vendors. Every vendor seems to have a different way to do it. This makes things really complicated when you want to move work to a new printer, split work across multiple different printers, batch jobs together, or even send work with inline finishing or tray pulls to a disaster recovery operation. I’ve seen operations keep hardware on the floor to run a single legacy job because of this.
This is an area where Solimar has done a lot of work. We can ingest almost any type of finishing information, add, remove or modify, and then output them to about any other method using Rubika. We can add finishing commands to files that never even had them, or even convert existing finishing commands into barcodes to drive offline finishing processes. This greatly simplifies moving work from one cut sheet device to another.
Most people moving to continuous feed are moving to full-color inkjet printers. This opens up a whole new set of possibilities for the work you’re currently producing with cut sheet printers. The first thing many companies want to do when getting a new inkjet is move to a white paper factory workflow. This typically involves replacing preprinted shells with electronic underlays. The white paper factory workflow is streamlined and requires very little human intervention. This saves huge money on things like warehousing and managing inventory of preprints. White paper factory workflows are great for disaster recovery or overflow printing to another white paper factory. Removes the dependency of inventory management for preprinted stocks. Reprints are simplified. Unlimited changes can be made to the digital preprints without the hassle and expense of physically reprinting them. If you need special marks or quality control pages, Rubika has you covered here, as well. Reversing the jobs print order digitally prior to print is less expensive and faster than using mechanical rewinders. Another task made really easy by Rubika.
When you get a new printer, you’re almost always increasing print volume and many times adding full-color. This usually means larger print files than before, sometimes much larger. These big files can bog down your prepress workflow and kill RIP times. Performance of your prepress and RIP workflows are more important than ever to support your new printer. One way to handle this is by buying more servers and just throwing hardware at it. Another way is to try to decrease the size and improve the efficiency of the bloated files bogging down your workflow by optimizing PDF within your workflow. PDF optimization does more than just make small files, although it does do that. You get granular capabilities to remove unwanted content, resample images, reorganize the objects in the file and make it go as fast as it can possibly go in your workflow, while maintaining your standards for quality. Data here is based on Keypoint Data UK lab tests on ReadyPDF. Unlike most optimizers, ReadyPDF was built ground up for transactional PDF files. If you haven’t tried it yet, you should give it a go.
Every operation has a system for submitting, routing and managing jobs when placing a new printer. It’s a good time to consider if your current solution will meet your future needs. Output management allows you to ingest, queue, route and manage work across multiple destinations in an automated way based upon business rules, and, or operator’s prerogative. This is key to being able to distribute work across your various assets to ensure you’re maximizing productivity for each type of job. Different, yet related, is an operational tracking dashboard. A dashboard integrates your automated, digital and physical workflows to monitor and track jobs and job related events as they happen. Prepress. postpress, shipping and beyond. Dashboards put a pretty face on your workflow by offering a web based interface for managing and tracking automated and manual processes within your workflow. An output management system only covers a subset of the digital workflow.
SOLitrack, as the name implies, tracks jobs, pieces and processes in your operation. Not only does it have a strong output management capability of its own, it works in concert with SPDE to make SPDE even more powerful as an output management solution.
Regardless of your output management or tracking solution, you still need to decide on the best way to communicate with your new printer. Our recommendation is to use a protocol that gives you bi-directional feedback from the printer. Printers that communicate in this way can report back on things like percent done, errors, and can even allow users to cancel and otherwise control a job while it is on press. With bi-directional printing, printers reports back that the job is completed and advances the workflow to the next step, automatically. It can also report on how long it took to print. Hot folders and other methods are fire and forget. Blind hand-offs in a workflow are so last century.
Visibility is probably the main reason for using a dashboard, but I think a close second is to collect data on the work going through your operations so that you can analyze and identify areas for process improvement. SOLitrack has extensive reporting capabilities for this purpose. If your output device supports it, it can also extract ink and media usage on a per job basis and report on it. For each work area in your operation, you can configure a monitor to show the folks there what work is due, past due, complete, and more. Since it only shows jobs that need to be processed in a specific area, like for example, cut sheet print, it is a burn down that helps the workers be more productive and engaged. Each activity in the workflow has to report what is happening to a central tracking system. This system uses a database to track and monitor what is happening to all of your jobs and production, and even after distribution by using mail tracking. SOLitrack can track jobs before they hit production, while they’re being produced, and after they’ve been shipped, tracking mail pieces all the way to a mailbox.
Thank you for your time. We hope you found this session helpful. Please feel free to reach out to us with any questions.
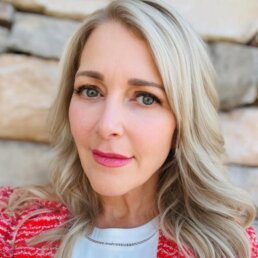